Many industries are incorporating digital twins with their avionics process, and the aviation industry is one of them. The digital twin can play a game-changer role in the aviation industry. Digital Twins can turn into the virtual form of an airplane or a part of an airplane and perform several operations on various levels to understand the possible result.
Digital Twin Development Company
It promptly suggests a solution if a pitfall in the system or an error occurs. It helps avoid possible situations and confirms the key to overcoming such issues. Digital Twins can easily forecast the likely traits that lead to accidental damage to the airplane.
RisingMax Inc. realizes the power of Digital Twins and their aspects of use in various sectors. RisingMax Inc. has successfully delivered more than 250+ software applications using technologies like artificial intelligence, machine learning, and big data. Just shoot your queries, and we’ve your answers!
Many aviation industries are looking forward to discovering the properties and features of digital twin technology. The aviation industry is looking forward to Digital Twins since it uses most technologies like the internet of things (IoT), sensors, big data, and artificial intelligence.

What Are The Use Cases of Digital Twin Aerospace?
The digital twin can present various opportunities for the aviation sector. It can help ensure the life of airplane parts and machines. Aviation companies can also use Digital Twins in the R&D sector. Digital Twin in aerospace can help examine and analyze the core development of the devices, parts, infrastructure, production unit, and much more to perform well. Digital Twin will be able to meet all standard norms, from quality checking to quality testing and provide excellent feedback with the solution.
“Digital Twin has noticed a 40% improvement in the parts and machines used with the help of digital twins.”
Digital Twins Bulletin
-
Research & Market says that the digital twin market is expected to grow from USD 6.9 billion in 2022 to USD 73.5 billion by 2027, at a CAGR of 60.6% during the forecast period.
-
Challenge has advised that a well-structured digital twin of an aircraft or a rocket ship would allow for tracking with 147% more accuracy that would follow the aircraft for longer proximities.
-
Data from IFS aviation customers over the last five years shows that 45 percent of all airline parts removals were unexpected, so the industry is in serious need of more intelligent predictions for maintenance on AOG faults.
How Digital Twins Are Revolutionizing Manufacturing And Smart Cities?
Benefits of Digital Twins In the Aerospace Sector
Digital Twins will revolutionize many industries, and the aviation sector is one of the primary aspects of the changes. There are several benefits of digital twins in the aerospace sector, some of which are quite impressive, which we will discuss here.
Development Of Equipment
The equipment development would greatly impact the aerospace sector because it eliminates the obstacles to increasing productivity and figuring out the processes. If the produced equipment is right, then this will make the whole system feasible.
Digital Twin uses big data and sensors to read and store the data effectively. If the system has any issues, then the digital twin forecast for the problem can be avoided before it occurs. This also enhances productivity and saves a lot of time.
Improve Efficiency
Digital Twin can perform testing within the system. It provokes improvements in the overall design. The testing phases can be delivered on several levels. It increases the equipment’s productivity and avoids any mishappening in the system.
Predictive Maintenance and Lifespan
Predictive maintenance ensures the machines and parts work smoothly and are well-tuned with the system. The feasible studies show the lifespan of the components or machinery, whether it is for reuse or needs to be scheduled for the maintenance phase. This enhances the capabilities of the system, and it informs of any potential threat in the system.
Virtual City Development In Metaverse
How Can Aerospace Industries Use Digital Twins?
- Digital Twins can improve and extend the parts and machines used in the aviation industries. It will enhance the use of parts and devices for the next iteration, saving time and money and keeping safety on priority. Boeing has witnessed a 40% improvement in using parts and machines in aviation.
- Digital Twin R&D can simulate the performance in various conditions, which impacts the improvement. Thus, the system will acknowledge itself at the time of the next repair, maintenance, and fixing of problems. This will improve the lifecycle of machines and parts. It also signifies robust solutions for any hazardous situation in the system.
- Digital Twin enhances the machines’ usability, enabling them to do things they could not do before. Digital Twins allows the system to monitor and produce 147% more accuracy. Performance tracking is one of the key advantages of using digital wins in the aerospace industry.

How Digital Twins Impact the Aerospace Industry
This is the digital era of Digital Twins and digital products. Most aerospace companies have started utilizing the fact to reduce the system’s downtime. Using digital Twins in aerospace can help predict and forecast any pitfalls that might arrive during the processing.
Digital Twins in the aerospace industry can work like a charm. Digital Twins can help connect with the physical modules; artificial intelligence will connect with the big data, and machine learning can enhance aerospace performance. It can forecast the weather and changes in the atmosphere and identifies any potential threat.
RisingMax Inc. has been introducing Digital Twins to several industries for the last 13+ years and is amongst the top US-based modern-age platform development companies. Knowing the benefits & facts, It has transformed many old established platforms into Digital Twins. It was a game-changer for their business. Let’s focus on yours!
Digital Twins Use Cases
Digital twins help forecast accurate and precise data about the determination of a system/parts/machine or a component that would not be able to perform anymore. And this is the perfect idea to suggest the system to point out the areas and improve or replace the existing system with a new one.
Such information is very helpful in improving performance, providing a resultant solution and saving time, and developing increased operational flexibilities. Studies of digital twin use cases in aerospace help find precise solutions that adhere to aerospace guidelines.
Let’s discuss a few use cases for a better explanation.
Boeing Digital Twins: Use Case1
Boeing, a famous aircraft-making industry, is well known for using digital twins. Boeing designs aircraft and their components. The use of digital twins is very helpful since it can easily predict the failure in the system, any issues in the plane, or the possibility of recovering a failed situation.
Boeing authorities have said that it has gained over 40% improvement in the development of parts and is continuously seeing amazing changes with the reports from development and the production team.
An example of Boeing’s used cases is to find the maximum exposure to reach cargo load balance. The digital twin can calculate the load time if an aircraft flies with a maximum overload of 50,000 kilograms. So, if the plane is going to fly less than the weight, it can.
The digital twin will show the stats by calculating with the help of IoT sensors and using big data. It helps aircraft not to get overloaded with weight, and it can add weight that will be paid off with the substantial charges with the courier services resulting rise in the profit of the company.
General Electronics Digital Twins: Use Case2
General Electronics has developed an engine using digital twin for its GE-60 aircraft. It is the world’s first-ever digital twin-based developed engine landing gear. Sensors are well placed at the landing gear points that provide information if there is an issue within the system or if there is a chance of fault or damage to landing gears.
GE has already built digital twin components for its GE60 Engine family and has helped develop the world’s first digital twin for an aircraft’s landing gear.
Sensors placed on specific landing gear failure points, such as hydraulic pressure and brake temperature, provide real-time data to help predict early malfunctions or diagnose the remaining lifecycle of the landing gear.
An example of such an issue could be a hydraulic pressure and brake in the temperature, causing malfunction or diagnosing the machine parts. So, it can work effectively while reusing, saving the time and cost of repairing the machine parts.
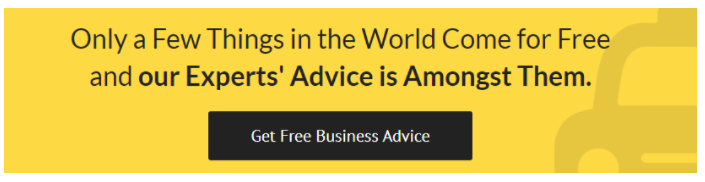
Develop A Digital Twin Or Replica Of University In Metaverse Web3
Digital Twin can help businesses unlock potential by retrieving the system’s data and forecasting what should be avoided, what should be done, and how it should be done.
It brings the approach to the best practices of Digital Twin to implement more feasible solutions. Artificial intelligence and machine learning programs, with the help of IoT, can do wonders for the aerospace industry.
If a digital twin is employed in a system, it can help predict which parts of machinery can be used and which should be avoided to meet a feasible solution.
This will help determine the choice of machinery and predict further issues like the maintenance schedules for a particular aircraft, which parts need to be changed, and the best practices to meet the standard norms.